Or how to build systems hoping that, just for once, they will never be needed…
Securing fuel cooling ponds, in case of pump prime loss, is a key component of our post-Fukushima operations. At Penly and Paluel, the Normandy Regional Division is building the main systems for the Backup Water Supplies (BWS) to tackle this major issue.
One process
For both nuclear power plants, the BWS works in the same way. The process involves building capable infrastructure, irrespective of events (earthquake, flood, etc.) to route water – via a gravity system, i.e. using zero energy – from the existing basins to the reactor buildings where the ponds are located. This makes the systems (HDPE ø160 PN25) fulfilling this emergency transfer function central to these security solutions.
Large-scale systems
At Penly, two 1,200m parallel pipes, buried at an average depth of 1.30m, are set up using 12m tubes assembled using electro-fusion welded sleeves, i.e. a little more than 200 tubes for just as many welds (a total of 2,400m). At Paluel, four 930m-long parallel pipes are set up using the same process, i.e. installing more than three hundred and ten 12m tubes over a total distance of 3,720m.
High structural standards
Given the sensitivity of this infrastructure, the tube welds are critical control points. So in addition to video inspection and 14-bar water-testing of the pipes, the welders and the welding method were pre-approved via decohesion testing.
A trencher and 2 shifts at Penly
Lying level with the site’s main road, the worksite’s laying rate has to be optimised. The selected option, which allows a rate of up to 144m/day, involves:
- a trencher that deconsolidates a 1,100m stretch of ground, at a depth varying from 1.30m to 3m, but leaves materials in place,
- a day shift that sets up 24m sections on the surface and welds the stretches laid in the trenches between them (4 welders),
- a night shift that excavates, lays 24m segments in the trenches, and backfills.
1 traditional, environmentally-friendly shift at Paluel
On this site, the topography requires traditional methods along the entire stretch. Sections stretching several hundred metres, pre-welded on the surface, will be laid in the trench as the earthworks progress. The pipes are buried at an average depth of 1.30m with special points at 3m and 7.5m. Here, environmentally-friendly processes are increasingly important and numerous measures to counter any potential incidents are required (work-specific transfer area, increased waste management, compliance with ZNIEFF (French natural zone of ecological interest, fauna and flora) requirements. These demands, in addition to documentary requirements and strict compliance with operating procedures and processes, clearly have an impact on work rates.
Designed and built to be used in case of a major incident, or even disaster, let’s hope that these BWS’s and their systems, despite their high functionality, will never need to be used.
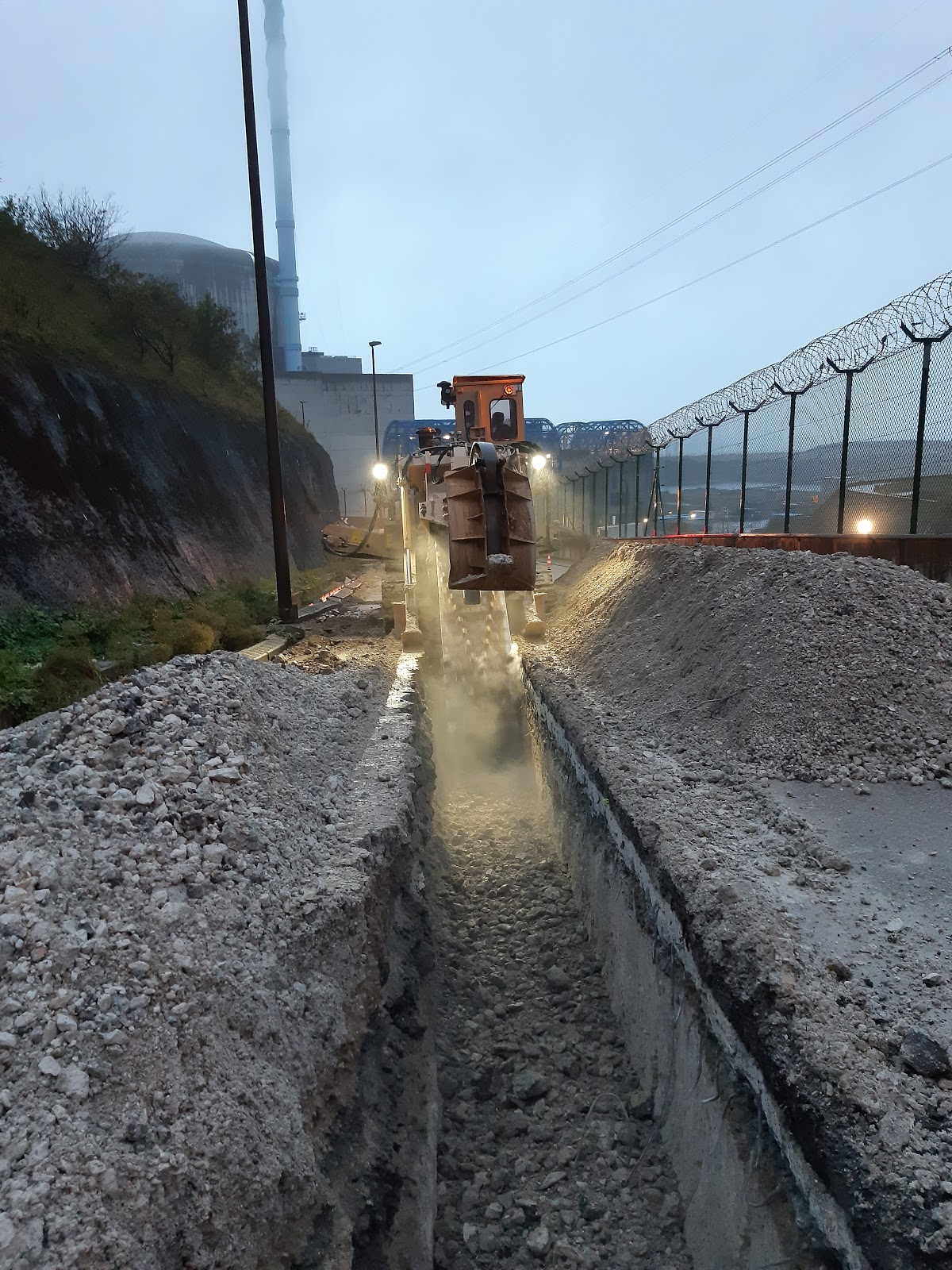